
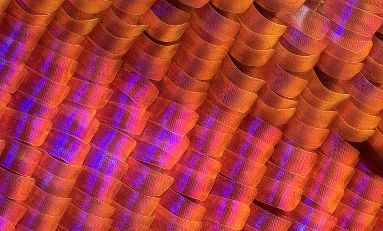
Nanopatterning for medical applications
6 September 2018
Nanotechnology appears in popular culture as a cure for everything from cancer to balding. In science nanotechnology is an umbrella…
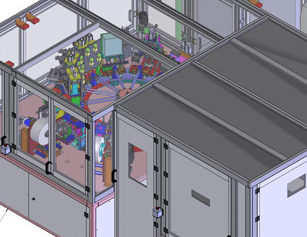
Consultancy or manufacturer?
12 December 2017
Let us suppose you need a new product developed. You have 3 choices: Develop the product entirely in-house. Contract a…
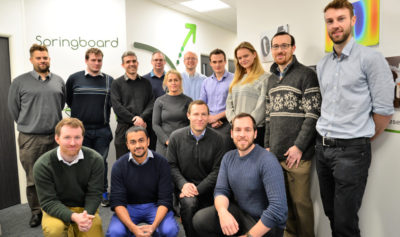
Springboard moves into new premises
26 October 2017
Fast-growing product and technology innovator Springboard has expanded into larger offices at St John’s Innovation Park in Cambridge, UK, having…
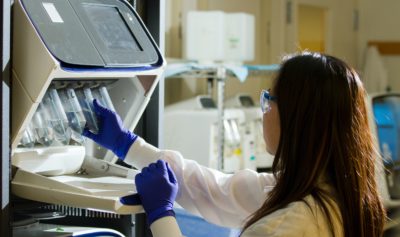
Massive demand for top medical device developers
22 December 2014
Springboard has been featured in a new article about the demand for top medical device developers. As a leading technology…
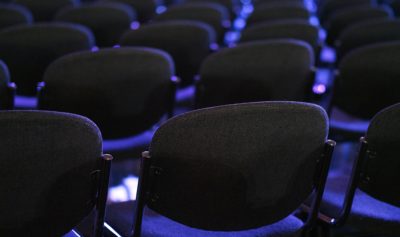
Springboard attending Wounds UK 2014
29 October 2014
The latest innovations in wound care will be on show at the Wounds UK Annual Conference in Harrogate, 10 – 12 November…
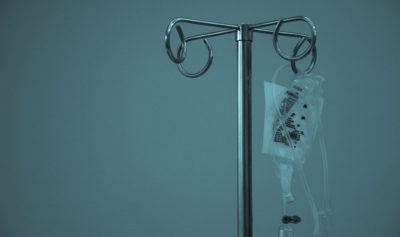
Top 3 devices from Trauma Innovation 2014
16 January 2014
I’ve just got back from the Trauma Innovation 2014 conference – Europe’s largest gathering of military, humanitarian and emergency healthcare…
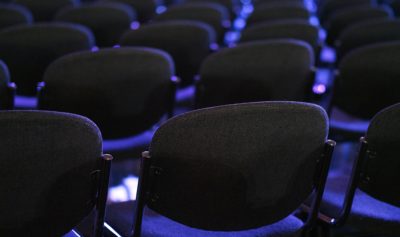
Springboard attending the Trauma Innovation Conference Jan 2014
8 January 2014
Springboard will be attending the forthcoming Trauma Innovation Conference in London at the Royal College of Surgeons on the 14th…
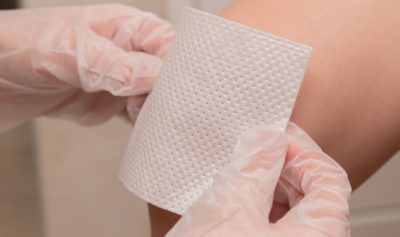
Where should innovation in Wound Care be focused in 2014?
6 January 2014
How can Wound Care technology companies grow their profits? Many of the answers to this question were on display recently…
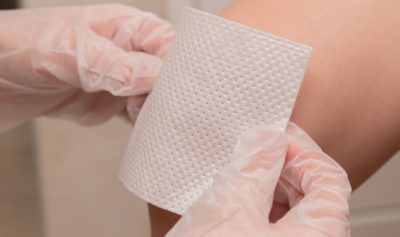
Springboard attending Wounds UK in Harrogate
5 November 2013
Springboard will be attending the UK’s leading Wound Tech conference in Harrogate from 11 to 13 November 2013. Wound care is…