
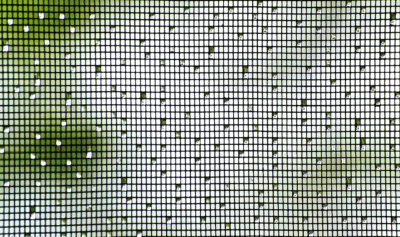
Superficial attraction: better membranes through surface science
6 March 2024
The importance of understanding surface properties Water is a multifaceted actor in our lives, being variously an ingredient in food,…
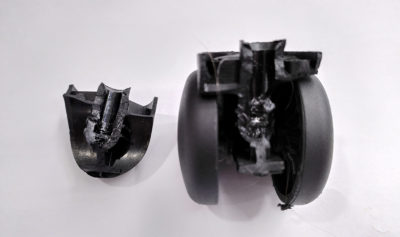
Mapping the fracture surface of an injection molded part
4 March 2024
Recently we had a wheel break off an office chair. Unlike many of our clients, we at Springboard get very…
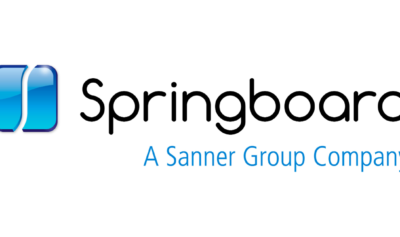
Sanner Group strengthens medical device design and development capabilities with the acquisition of Springboard Pro
3 January 2024
Sanner Group, a leading global healthcare packaging manufacturer and medical device Contract Development and Manufacturing Organisation (CDMO) has acquired Springboard,…
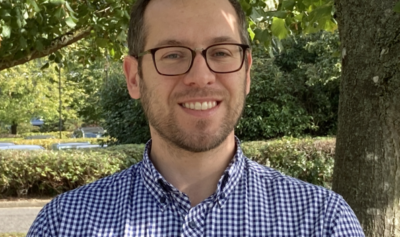
Springboard strengthens drug delivery and biotech R&D service by welcoming Alex Vasiev to the team
17 October 2023
Springboard Pro, a leading engineering consultancy company based in Cambridge, UK, is pleased to announce the addition of Alex Vasiev…
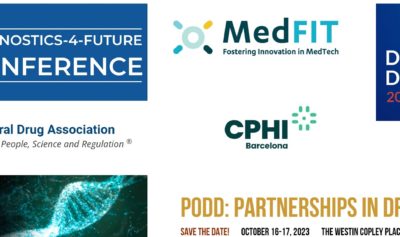
October heralds the return of the event calendar!
11 September 2023
October sees the return of the event calendar after the summer break and Springboard is attending multiple events across the…
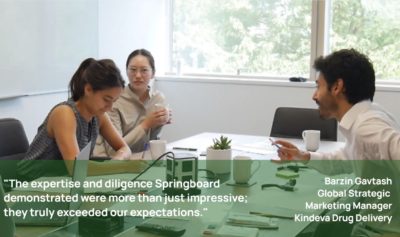
How can Springboard help you with your device design? Find out today
2 August 2023
Find out how Springboard has helped clients to design and deliver devices and take a look at the facilities at…
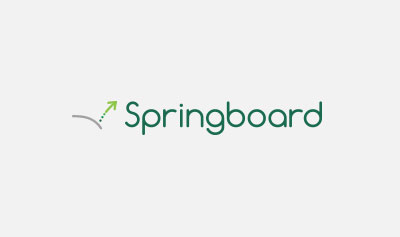
Springboard bolsters electronic engineering department with new hire
24 January 2023
Springboard has announced that they have welcomed Mike Beck to the electronic engineering team. Mike brings with him 3 years’…
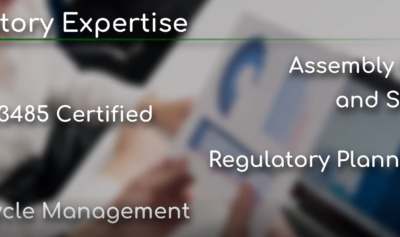
Walk through Springboard project process and facilities
8 November 2022
We’re proud of the work that we do, and each and every project goes through a stringent process, starting with…
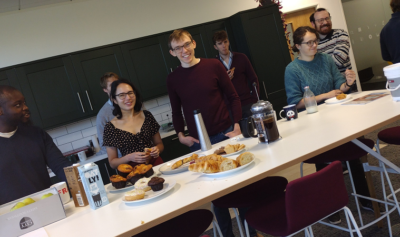
Managing mental health
10 October 2022
Mental health is a topic that we take very seriously and no less so than on national mental health awareness…