Using 3D Resin Printers for Early Product Design
11 March 2024
Rapid Prototyping with 3D Printers
Stereolithography (SLA) 3D printing can be a powerful tool when working on early-stage product design. Being able to iteratively prototype the high-risk elements of a product allows for the development of a more robust design overall, while minimising the time to market. But, as with any tool, we need to understand the limits of its capabilities to get the best use out of it.
At Springboard, we recently worked on a device requiring small complex geometries which also needed to be resistant to high temperatures. SLA printing was an invaluable asset in the feasibility testing stages as it allowed us to test a wide range of different ideas in a short space of time. We were also able to use a special high temperature resin for parts of our design, although this came with its own set of challenges.
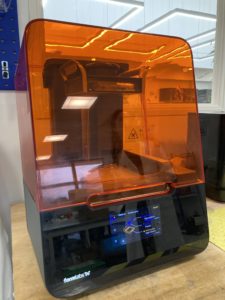
3D Resin printer
What are the benefits of SLA printing?
SLA printers are favoured across many sectors, from jewellery making, to dental prosthetics, to prototyping, and the advantages are well documented:
- High accuracy and consistency of printed parts: SLA printers can produce parts with good dimensional accuracy, which is crucial where precise measurements are required (such as in medical devices)
- High resolution allows more intricate designs with fine details, useful for small or complex geometries
- Wide range of high performing engineering materials available to provide the mechanical or aesthetic properties required (high temperature resistance, strong parts, ESD, transparent parts, etc.) making it a very versatile tool
- Faster manufacture of complex geometries than traditional machining or rapid prototyping methods
- Smooth surface finish: parts often come out of the printer with a smooth surface finish that can require little to no post processing, especially compared to other 3D printing processes such as FDM (fused deposition modelling)
What are the drawbacks of SLA printing?
No process is perfect, so it is important to understand what the drawbacks are:
- Cost of both the resin itself and all accompanying materials needed is significantly higher than the more common FDM approach. Resins start at around £150 per litre and each type of resin needs their own tank (£144) which needs to be frequently replaced. Additional costs include cleaning fluids and PPE.
- Space, storage, and waste: resins are UV sensitive so must be stored accordingly, plus the additional chemicals needed for cleaning and associated PPE. The waste is also more difficult to maintain safely and dispose of properly.
- Post processing is also much more involved than other 3D printing methods, as parts require cleaning in IPA (Isopropyl alcohol) or other chemicals.
- Time: while the parts themselves can print much faster than FDM, some resins can take as long as two further hours to cure. Printing multiple parts in one go may feel like a breeze, but especially intricate parts can still take several hours to print. The post processing is labour intensive as it includes cleaning off resin – which can get messy!
- Support structure is still needed in SLA printing, which leave marks and can risk damage to delicate parts during removal.
- Warping of parts during the UV curing step is not uncommon, although this can be controlled to an extent through geometry and design features.
- Discolouration of parts during the UV curing step or after, as parts may remain UV sensitive, can be a concern if parts are needed for aesthetic purposes such as prototypes for presentations.
Some handy tips when using a 3D resin printer
Over the course of this particular design project, we spent a lot of time using the SLA printer and developed some insights into the process. Rather than simply listing the pros and cons, we also consider some lessons learned that we found SLA printing, and our work overall, more successful:
- Printing lots of iterations of a design quickly does not replace a good design review. It can be better to take a step back and assess the problem as a whole, rather than test several iterations of a design with minor changes.
- Good cleaning of the part before curing can make a big difference in the quality of the finished part – especially small complex part when excess resin collects.
- Understanding the resin properties is important. If a design works well in one type of resin, it may not work well in another as the resins behave differently, e.g. some are prone to more warping when cured.
- It’s important to keep in mind that SLA printing will not be the final manufacture method. Tolerancing and some design features may have to evolve further down the line, but it is always best to realistically design for manufacture as early as possible.
Do you have a project that could benefit from rapid prototyping? If so, get in touch today to find out how we can help.
– Elena Gus Tarazona and Kiara Taylor.